In the manufacturing world, understanding what is capacity utilization is essential for achieving operational excellence and boosting both efficiency and profitability. Capacity utilization reflects the balance between the production level currently achieved and the potential output that could be reached without additional capital expenditure. Manufacturers can significantly improve their operations by optimizing capacity utilization, from minimizing waste to maximizing output. Below, we examine the key role that capacity utilization plays in the manufacturing sector.
Impact of Capacity Utilization on Operational Efficiency
Alt text: Two professionals are discussing the topic of ‘what is capacity utilization’ and how it impacts operational efficiency.
Operational efficiency in manufacturing is profoundly affected by how well a company utilizes its capacity. Production processes are optimized, costs are kept at bay, and operations have minimal downtime when utilized effectively. On the contrary, poor capacity utilization can lead to increased operational costs and reduced efficiency.
Efficiency impacts are also tied to energy consumption and staffing. Machines running below their optimal capacity can still consume the same amount of energy as when they’re at peak performance, thus leading to waste. Similarly, a workforce operating under reduced capacity may not be employed to its full potential, affecting labor costs and productivity.
For operational efficiency, manufacturers must strive for a balanced approach. Excessive focus on high utilization can lead to machinery wear-and-tear and overworked employees, while insufficient utilization suggests that resources are not being used effectively. Therefore, targeting an optimal level that maximizes output while maintaining resource health is crucial.
Continuous monitoring allows for swift adjustments in manufacturing processes, ensuring that plants operate at levels that promote efficiency and longevity. Advanced predictive analytics tools can help managers make proactive decisions, sustaining an optimal balance in capacity utilization.
Capacity Utilization and Its Role in Cost Management
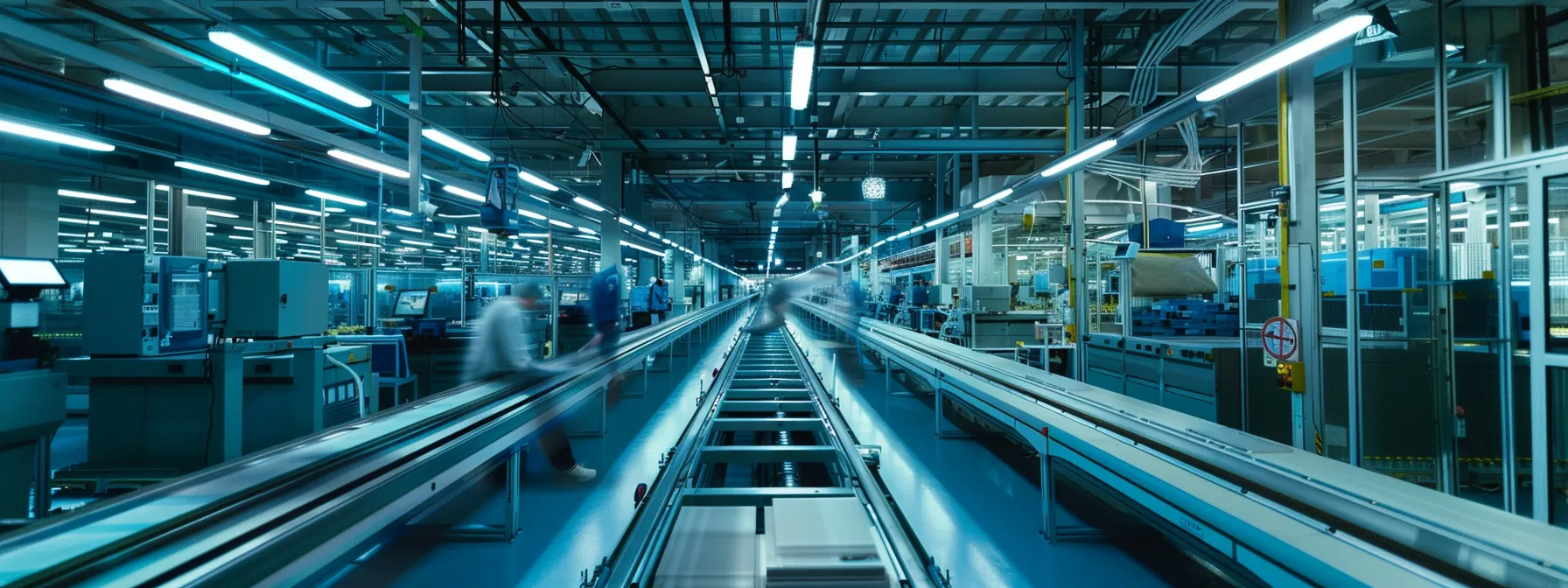
Alt text: A picture of manufacturing illustrating capacity utilization and its role in cost management.
Cost management is another crucial aspect directly influenced by capacity utilization within manufacturing industries. When capacity is effectively utilized, manufacturers can dilute fixed costs over a larger output, lowering the unit cost of production. This production efficiency reflects positively on the bottom line.
However, when there’s excess capacity, the burden of fixed costs such as rent, utilities, and salaries remains constant despite the lower output, which drives up unit costs. This situation can make manufacturers less competitive, as they cannot realize economies of scale.
Understanding and carefully managing capacity utilization can be a powerful tool in cost control. By optimizing existing resources, manufacturers can avoid the pitfall of unnecessary expansions or expensive investments to increase capacities that are not yet required.
Lean manufacturing principles often consider capacity utilization, striving to eliminate waste in processes, including wasted capacity. Manufacturers can maintain tighter control over production costs by continuously seeking ways to improve operations and increase utilization.
Strategic Planning: Optimizing Capacity for Market Demand
Strategic planning takes a forward-looking approach to capacity utilization, aligning current production capabilities with future market demands. Manufacturers must anticipate changes in consumer preferences, economic trends, and technological advancements to ensure their capacity utilization aligns with these shifts.
Manufacturers can respond more rapidly and effectively to demand increases without significant capital expenditures by optimizing capacity. This agility offers a considerable competitive advantage, enabling quick adaptation to market changes while maintaining cost efficiency.
A delicate balance is required in strategic planning as overestimating future demand can lead to overinvestment and unwarranted high levels of unused capacity. Conversely, underestimating can result in lost opportunities and customer dissatisfaction due to an inability to meet demand. Accurate forecasting is essential to mitigate these risks.
Incorporating capacity utilization into strategic planning can offer manufacturers insight into how to make calculated risk assessments. It guides them in optimizing their operations, ensuring adequate capacity is available to meet current and prospective customer requirements.
Overall, effectively managing capacity utilization is essential for maximizing operational efficiency and controlling costs in the manufacturing sector. By strategically balancing production levels with market demands and continuously monitoring performance, manufacturers can enhance their competitiveness, reduce waste, and ensure that resources are used optimally. This approach improves immediate operational outcomes and supports long-term sustainability and growth.